
Then I begin to block with 180 grit on the biggest and most appropriate block that fits the shape of the surface I'm blocking.

After blocking the epoxy I know the areas where peppered spray droplets are my low spots and the bare metal are my high spots. I work the panel in many differing ways depending on the situation encountered. In this instance I started with a body hammer and bean bag behind it,
gently hammering it straight.

There's was also some very slight highs that just needed to be bumped down with a dinging spoon.

Once you have it straight you can smooth it out with a hammer and dolly, planishing hammer, or whatever tickles your fancy. I chose to use a dolly with a 2.5" tear drop mallet with the head flattened.

Once you're done with metalwork you can now prep the panel for filler. A da with 80 grit will work fine.

Now we move onto the filler stage. My philosophy is to metal work it a little better so I can always get my filler work done in two applications. On most occasions I pull it off. The first round of filler I'm not concerned about leaving deep scratches and I also know a 40 grit scratch cuts faster and straighter than 80 grit so that's where I start.
An air file is a great tool for cutting down time and cutting stuff down flat but you gotta know how to use it and where not to use it. As you can see I stayed away from the compound curves. I'll save those for hand blocks and I always save some filler for hand blocking anyways when I use my air file.

After using my air file I switched over to blocks and addressed the compound curves.


40 grit can be deceiving in that it will clog on you and be a hassle to unclog but the truth is the paper is tough and and can be groomed a few times before it actually gets dull.

The hardest area to block is the corner. So after I use my cut down block to initially address it, I smooth it out with a soft block thereafter.
After all the 40 grit sanding is complete you may have some small imperfections. The time is now to deal with them cause you want your top coat AND primer to be pinhole free and easy to sand.
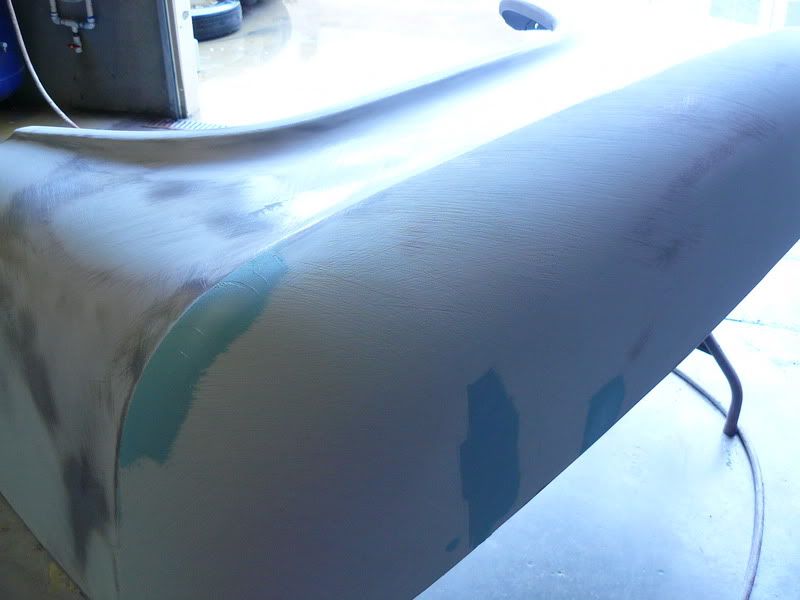
Now it's time for your final coat. I want to make sure I expose any pinholes at this point so I use air and a wire drill bit.
Next I tape my bodyline so I get a nice perfect line. For my final coat I use 50% good filler with 50% 2k polyester glaze. Extra emphasis on thin coats!
Then I remove the tape before it hardens and lifts. I do not
want to sand with the tape on for this situation.
I then sand the top with 80 grit. After that's sanded I have other
areas that need their final coat of filler on the opposite side of the
body line. I then tape on the other side of the body line and apply
filler to those areas. I then remove the tape and re apply new
tape when it's dry and ready to sand.
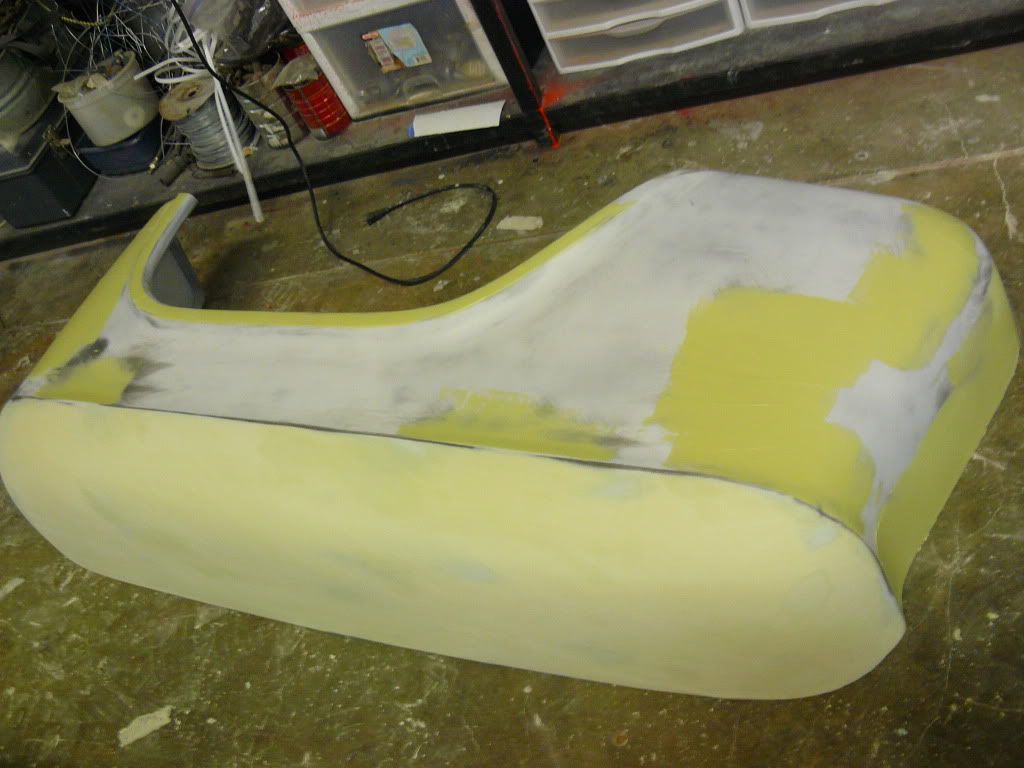
After sanding, guide coat all your filler and sand with 180. Last, you
da sand with 180 on your 40 grit scratches on the surrounding areas(not filler!). This
will help buffer the scratches out for primer.
No comments:
Post a Comment